Manufacturing is a process of transforming raw materials or components into finalized products by utilizing tools, manual work, machinery, and chemical procedures.
Manufacturing enables businesses to sell their products at a higher price than the initial cost of the materials used. By utilizing assembly line processes and advanced technologies, large-scale manufacturing allows for the mass production of goods.
Through efficient manufacturing techniques, manufacturers can take advantage of economies of scale, producing a greater number of units at a reduced cost.
Manufacturing Explanation

Manufacturing is an essential part of the economy and involves converting raw materials into finished goods. This process includes the production of various items like metal products, furniture, and packaged food.
Converting raw materials into useful products adds value and increases prices, making manufacturing profitable. Some individuals have specialized skills in manufacturing, while others provide funds for businesses to acquire tools and materials.
As mentioned earlier, increased efficiency in the manufacturing process can result in improved productivity and reduced costs. Manufacturers can achieve this by being capable of:
- Reducing redundancies
- Improving work quality
- Updating equipment and procedures
- Setting realistic goals
- Streamlining intake, supply chain, and distribution channels
Economists frequently analyze manufacturing, and the conference board frequently provides reports on this industry.
Manufacturing Type
The process of manufacturing products has evolved throughout history. In the past, people used raw materials to create goods, and in some situations, this practice still exists. Hand manufacturing refers to the use of simple tools and traditional methods to produce items. This type of manufacturing is commonly linked to decorative art, textile production, leatherwork, carpentry, and certain forms of metalwork.
Handmade products require a lot of time and effort, leading to varying prices. Unique handmade fashion items are usually more expensive than mass-produced ones. However, some producers of handmade goods may be exploited in regions with weak labor laws and high unemployment rates.
Bigger corporations employ mechanization to produce a large quantity of items. This method relies on the use of machines, eliminating the need for manual handling of materials. The production process requires minimal human labor, except for the presence of skilled individuals who are responsible for operating and maintaining the machinery.
Additive manufacturing
This particular method of production is often known as 3D printing. It entails the gradual construction of layers on top of one another to form shapes and designs in a three-dimensional manner, utilizing a specialized device like a 3D printer.
Modernized Production
This approach utilizes innovative technologies to enhance the manufacturing procedure. By leveraging these technologies, companies can enhance the quality and usefulness of the materials they utilize, thereby catering more effectively to their target markets. Additionally, these newer technologies facilitate quicker introduction of new products to the market while simultaneously increasing production.
Contract Manufacturing
In the manufacturing industry, it is common for companies to establish partnerships and business relationships with other firms in order to delegate specific manufacturing processes. For instance, an automotive company might collaborate with a third-party organization to produce components that they will incorporate into their assembly lines for car manufacturing.
Types of Manufacturing Techniques
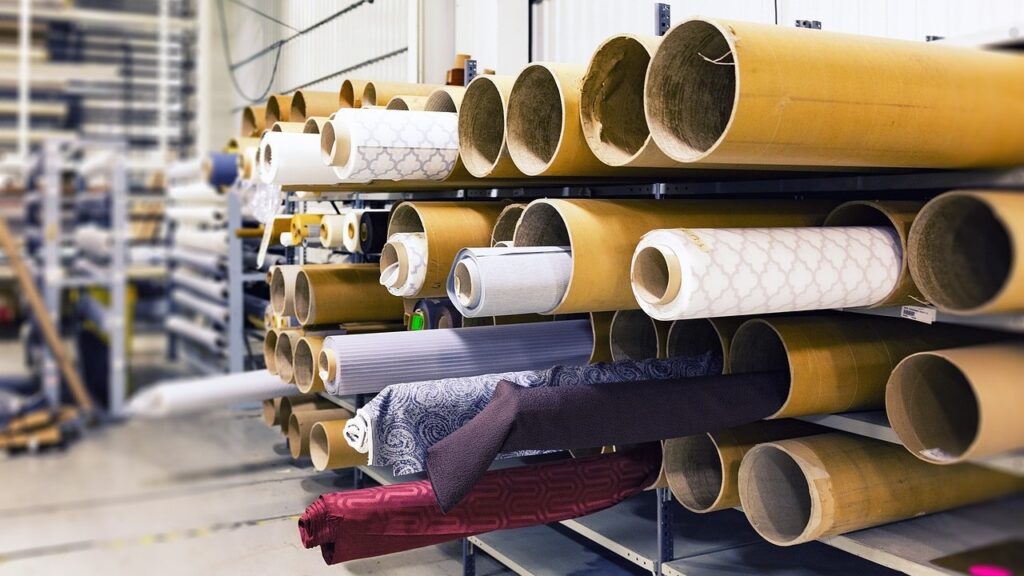
Make to Stock (MTS)
The conventional method of production is known as make-to-stock, where a company produces a standardized product based on predicted demand. The company predicts the number of units that will be sold within a specific timeframe and prepares in advance to manufacture that quantity of goods. These goods are typically stored as inventory until they are ready to be released and distributed widely.
One benefit of MTS is that companies can take advantage of economies of scale. By determining a specific level of production, a company can carefully plan and anticipate the required amount of raw materials, labor, and equipment, resulting in efficient manufacturing plans. However, failing to meet these expectations can lead to wasted products, excess inventory, and fixed costs that are committed but not fully utilized.
Make to Order (MTO)
Make-to-order manufacturing is a different approach than MTS. It involves collaborating closely with the customer to comprehend their requirements and desired specifications for the product. Manufacturing activities are usually initiated only after a contract or letter of intent is signed. While manufacturers may create basic prototypes, they typically delay starting the actual manufacturing process until they receive complete and detailed product specifications.
Made-to-Order (MTO) is commonly seen in industries that produce specialized products with a specific purpose. Sectors such as aerospace, construction, and technology (to a lesser extent) often refrain from manufacturing goods until they receive confirmation of a purchase from a government entity for aircraft or a long-term lease agreement signed by a tenant.
MTO manufacturers have the advantage of being able to charge higher prices for their products because they are not easily available in the market, especially if they are highly specialized. Additionally, MTO manufacturers only produce goods when there is a confirmed sale, so they do not need to maintain inventory. However, a disadvantage of MTO manufacturing is that it can lead to fluctuating product demand, resulting in slower periods of business.
Make to Assemble (MTA)
Another type of manufacturing technique is known as make-to-assemble process, where companies adopt a strategy of initiating the production of individual parts in advance. Later, when customers start placing orders, these companies assemble the already manufactured components to fulfill the orders.
The company can deliver products faster with its current manufacturing process, but there is a risk of having excess inventory if demand is lower than expected. Additionally, trying to find a balance between different manufacturing processes may result in losing the benefits of each approach.
Types of Manufacturing Processes
In conclusion, the manufacturing process can be categorized into various production methods, and each method yields a distinct and exclusive final product.
Discrete manufacturing
The term “discrete manufacturing” is used because each manufactured product is unique and can be easily identified. To keep track of the materials used in each individual unit, a bill of materials is used in the manufacturing process. In discrete manufacturing, production is often done on an assembly line, where workers follow a set schedule and record the materials used.
Process Manufacturing
The text explains that there are two main types of process manufacturing. The first category is batch process manufacturing, which involves making a product based on a specific standard and recipe. This method is commonly used in the food and beverage industry to create consistent products in a specific quantity.
Continuous process manufacturing refers to the consistent and ongoing operations that involve manufacturing a product continuously for an extended period. However, there may be temporary pauses in the manufacturing process before it resumes. This type of manufacturing is commonly used in the oil and gas industry for extracting natural resources through drilling.
Mixed mode manufacturing
Certain products may involve a blend of discrete and manufacturing procedures. This commonly occurs when goods are produced in batches and then transformed into distinct individual packages. Initially, the creation of the product involves manufacturing processes, and in the latter part, the specific details related to the delivery method, such as any customer customizations, are incorporated.
Job Shop Manufacturing
Job shop manufacturing is a method used when a company needs to produce a batch of goods different from their usual products. It involves unique setup and processing steps, including modifying equipment for the specific product being manufactured.
Repetitive manufacturing
Repetitive manufacturing is a process where long manufacturing processes are divided into smaller parts. Each part is responsible for manufacturing a specific component, which is immediately transferred to the next assembly line. Temporary storage areas are not used in this process.
History of Modern Manufacturing
Prior to the Industrial Revolution, the market was primarily filled with products that were made by hand. However, this all changed with the advent of the Industrial Revolution, which introduced a new manufacturing process where raw materials were transformed into finished goods on a large scale.
With the introduction of steam engines and other advanced technologies, companies were able to incorporate machines into their production process. As a result, there was a decrease in the reliance on human labor and a significant increase in the quantity of goods that could be produced.
The introduction of mass production and assembly line manufacturing revolutionized the way companies produced goods. This new method enabled companies to produce standardized parts that could be easily interchanged, eliminating the need for customized parts. As a result, finished products could be manufactured more efficiently, with the process being significantly streamlined. Ford played a significant role in popularizing this mass-production.
With the advent of computers and precision electronic equipment, companies have been able to develop advanced manufacturing techniques. These methods are often associated with higher costs due to the need for specialized labor and increased capital investment.
Over the years, the skill set needed for operating machines and creating manufacturing processes has seen significant changes. Due to the lower cost of labor, many manufacturing jobs that do not require advanced skills have moved from developed countries to developing countries. Consequently, developed economies tend to focus on producing high-quality products that demand precision and expertise in manufacturing.
Measuring Manufacturing in the Economy
Economists and statisticians working for the government utilize different ratios to assess the significance of manufacturing in the economy. One of these ratios is manufacturing value added (MVA), which measures the manufacturing output of an economy in relation to its total size. This ratio is expressed as a percentage of the country’s gross domestic product (GDP).
The Institute for Supply Management (ISM) surveys manufacturing companies to gather data on employment, inventories, and new orders. This data is published monthly in the ISM Manufacturing Report, which is closely followed by financial analysts and researchers as it is seen as a possible early indicator of the economy’s health and the stock market’s direction.
Manufacturing has consistently played a significant role in the economic growth of the United States. According to estimates, the manufacturing sector contributed approximately 10.8% to the country’s Gross Domestic Product (GDP) in 2020, amounting to a substantial sum of over $2.2 trillion.
Manufacturing process steps
These seven steps cover the entire process of creating a product, including the preparation and completion stages, in addition to the actual manufacturing of the physical item.
1. Come up with an idea
The process of manufacturing starts with the development of ideas and the creation of a vision for the product. This vision determines the nature of the product, the intended audience, the purpose of the product, and the competition in the market. These questions play a crucial role in shaping the product and determining its features.
2. Conduct a thorough analysis
Manufacturing involves more than just physical production; it also includes conducting research to enhance the product, such as studying raw materials, equipment, production conditions, and ways to differentiate from competitors.
3. Create the product’s design
After taking research factors into account, the next step is to create the product design. It is crucial to consider the needs and usage of the customers while designing. Additionally, any manufacturing limitations identified during the research phase should be incorporated. Understanding the costs associated with the product design is essential for forecasting its profitability. This stage is where the manufacturing process is strongly influenced by research and development.
4. Complete and create a final version
After completing the design stage, it is now necessary to make final determinations regarding the product. This involves selecting the appropriate raw materials to use and determining how the manufacturing process will be defined. These decisions are put into action by creating an initial prototype. This entails creating a smaller version of the product for testing purposes, which closely resembles the final manufactured product.
5. Involves conducting prototype testing
After finishing the prototype, the next step is to conduct tests on it. These tests involve examining the real resources used in the product to gain a better understanding of the actual cost and potential profit margin. Additionally, these tests aim to identify any weaknesses or inefficiencies in the manufacturing process.
This stage typically occurs just before mass production commences. Although adjustments can still be made later on, this is the opportune time to make significant changes that won’t have major consequences on the product or manufacturing process.
6. Produce the Product
After conducting sufficient amounts of time, testing, and research, it is now the appropriate moment to commence production. The company procures the required machinery and equipment to establish a complete manufacturing process for producing the goods. Additionally, the company makes investments in the total workforce, storage facilities, insurance, and other expenses associated with operating a complete manufacturing line.
Instead of going back to the initial stages of prototyping, companies have the option to constantly enhance their processes by making smaller changes during the manufacturing phase.
7. Keep an eye on Goals
To ensure ongoing improvement, it is necessary for the company to consistently assess the progress and determine if the set expectations are being achieved. This involves analyzing the production costs of the product and comparing them to the selling prices. Additionally, the company needs to evaluate the level of demand for the product and adjust the scale of production accordingly, depending on consumer preferences.
Comparison between Manufacturing and Production
While they are often used interchangeably, there are slight distinctions between the manufacturing process and the production process. In manufacturing, a company typically needs to acquire raw materials from external vendors in order to transform them into final products. On the other hand, in production, the company usually possesses the raw materials themselves.
The meaning of each term involves various procedures. Production has a wider scope and includes manufacturing, as it involves the conversion of input into output. On the other hand, manufacturing is a more specific form of production that focuses on taking raw materials and turning them into tangible finished products.
The process of manufacturing concludes when a physical product is created. However, in some cases, production can result in either a physical or non-physical product. For instance, let’s take the example of a theatrical performance. A show or theater production comes to an end with the presentation of entertainment that is meant to be enjoyed by the general public.
The manufacturing process heavily depends on the availability of raw materials and the use of heavy machinery or equipment. It also requires the allocation of time and labor to set up the process. However, the need for machinery during production may vary depending on the desired output.
Manufacturing
- Requires procurement of raw material
- Output is physical, tangible goods
- Machinery and labor are essential
- More specific type of process
Production
- Previous ownership of inputs is often necessary
- Output can be tangible or intangible
- Machinery may or may not be needed
- It is a less specific type of process
Example of Manufacturing
Toyota Motor Corporation, a successful manufacturer known for its efficient manufacturing process, plans to increase its long-term forecast of battery electric vehicle sales. They aim to sell 3.5 million units by 2030, up from the previous plan of 2.0 million.